Commercial Elevators in Washington
Primarius Elevator
provides complete lines of: traction, hydraulic, machine room less (MRL), modular, wheel chair lifts, dumbwaiters, material lifts
and freight elevators
in a variety of speeds and sizes. We offer a wide range of options to meet specific needs and requirements of the project. Our goal is to become your trusted advisor in selecting the right options for your application, including: finishes, styles
for you elevator cab, entrances and signal fixtures.
In Ground Hydraulic
This is the traditional design used for decades. It utilizes a single-stage hydraulic jack installed in the ground. The jack is located directly under the car, near the center of the platform.
Advantages:
Advantages:
- Usually the lowest material cost application.
- Accommodates front and rear openings in any configuration.
- No extensive pit or overhead is required.
- Available for both low and high capacity cars.
- Easy to install.
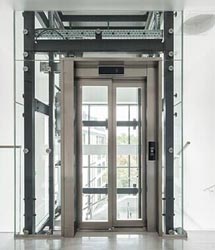
Disadvantages:
- Oil contamination in the ground is possible. As a precaution, the jack can be enclosed in PVC pipe. Areas with frequent seismic activity will have the greatest risk of oil contamination.
- The jack must go down into the ground roughly the same distance as the desired travel (multi-stage jacks can reduce this distance). Drilling a jack hole is expensive and may be nearly impossible in certain structural or geologic conditions.
- 79 ft. maximum travel distance
We offer a full line of Holeless and Holed (in ground) Hydraulic elevators, traction and MRL (Machine Room Less) elevators.
Examples of Elevator Plans
In Ground, Rear/Slide Slung
This application is used when a side opening is required in addition to a front opening. The rails and brackets are located on one wall of the hoistway. Please call Primarius Elevator for job-specific dimensions.
Advantages:
Advantages:
- Accommodates front and side openings.
- No extensive pit or overhead is required.
- Available for both low and high capacity cars.
- Since the rail brackets are all mounted on one wall, additional rail force accommodations may be necessary.
- Oil contamination in the ground is possible. As a precaution, the jack can be enclosed in PVC pipe. Areas with frequent seismic activity will have the greatest risk of oil contamination.
- The jack must go down into the ground roughly the same distance as the desired travel (multi-stage jacks can reduce this distance). Drilling a jack hole is expensive and may be nearly impossible in certain structural or geologic conditions.
Twin Post Holeless
This design utilizes two hydraulic jacks and provides maximum structural stability. The jacks, located on each side of the car, are either single-stage or telescopic. The appropriate jack type is determined by the amount of travel and the project conditions. The single-stage jacks are popular for two-stop arrangements, while telescopic jacks are generally used for three and four stop projects.
Advantages:
Advantages:
- No jack hole is required. This eliminates the cost of drilling and the risk of oil contamination.
- Accommodates front and rear openings in any configuration.
- Available for both low and high capacity cars.
- Usually requires more overhead than an In-Ground project. The greater the travel, the greater the overhead must be.
- Requires a wider hoistway for the jacks.
- The material cost is typically higher than that of an In-Ground package.
Roped Hydraulic
This is a holeless design limited to low capacity applications. Wire ropes are utilized in conjunction with a hydraulic jack to lift the car at a 1:2 ratio. For every foot that the jack rises, the car rises two feet. The jack and rail equipment is mounted either to the side or to the rear of the car, depending upon the opening configuration.
Advantages:
Advantages:
- No jack hole is required even though the travel can be as great as 100 feet. Without a jack in the ground, the risk of oil contamination is eliminated.
- Front & side openings can be easily accommodated.
- No extensive pit or overhead is required.
- Because the rail and jack equipment is located either at one side of the car or at the rear, additional space is required at that location.
- Since the rail brackets are all mounted on one wall, considerable rail force accommodations are necessary.
- The installation time is greater than that of an In-Ground application.
Twin Jack Roped Hydraulic
This design utilizes wire ropes in conjunction with two hydraulic jacks to lift the car at a 1:2 ratio. For every foot that the jacks rise, the car rises two feet. The use of two jacks, one on each side of the car, provides maximum structural stability.
Advantages
Advantages
- No jack holes are required even though the travel can be as great as 100 feet. Without any jacks in the ground, the risk of oil contamination is eliminated.
- Accommodates front and rear openings in any configuration.
- Available for both low and high capacity cars.
- No extensive pit or overhead is required.
- Large platform designs and high capacity projects can be accommodated.
- Requires a wider hoistway for the jacks and roped equipment.
- The installation time is greater than that of an In-Ground application.
Traction
This design utilizes a geared machine, ropes, and counterweights instead of hydraulic equipment. The main guide rails are mounted on each side of the car and an additional pair of counterweight rails is located on one side or at the rear. The geared machine, along with the related drive equipment, is generally located above the hoistway in a penthouse machine room. In some limited situations, it can be located next to the hoistway at a lower landing. This latter arrangement is referred to as a basement traction.
Advantages:
- No risk of oil contamination to the ground.
- Accommodates front and rear openings in any configuration.
- Available for both low and high capacity cars.
- Nearly unlimited floor travel is possible.
- Has greater power efficiency than hydraulic applications.
- Allows significantly higher car speeds than hydraulic designs.
Disadvantages:
- The material cost is substantially higher than that of hydraulic applications.
- There are structural building considerations because the elevator is supported by the top of the hoistway.
- Elevator maintenance cost is generally greater than that of hydraulic elevators.
- Cycle time for securing the material package and installing it is generally longer than that of hydraulic elevators.
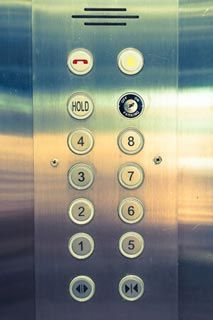
Traction, MRL
This design utilizes a gearless machine, ropes, and counterweights instead of hydraulic equipment. The main guide rails are mounted on each side of the car and an additional pair of counterweight rails is located on one side or at the rear.
Advantages:
- No risk of oil contamination to the ground
- Accommodates front and rear openings in any configuration
- Has greater power efficiency than hydraulic applications
- Allows significantly higher car speeds than hydraulic designs
Disadvantages:
- The material cost is substantially higher than that of hydraulic applications
- There are structural building considerations because the equipment is all mounted inside the hoistway
- Elevator maintenance cost is generally greater than that of hydraulic elevators
- Cycle time for securing the material package and installing it is generally longer than that of hydraulic
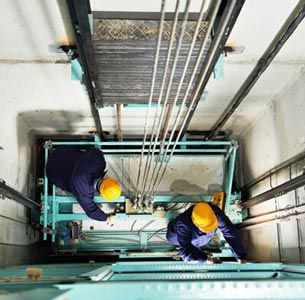
LULA (limited use/limited application) Elevators
LULA elevators (limited use/limited application) are ideal elevators for energy conscious consumers or clients who have architectural limitations.
This type of elevator is designed with efficiency in mind, allowing for versatile elevators that need to fit in smaller than ideal spaces within a building's floor plan limitations. The unique designs require less physical space for all of the machinery needed to operate an elevator, allowing for smaller elevators to be installed in smaller spaces.
This type of elevator is designed with efficiency in mind, allowing for versatile elevators that need to fit in smaller than ideal spaces within a building's floor plan limitations. The unique designs require less physical space for all of the machinery needed to operate an elevator, allowing for smaller elevators to be installed in smaller spaces.